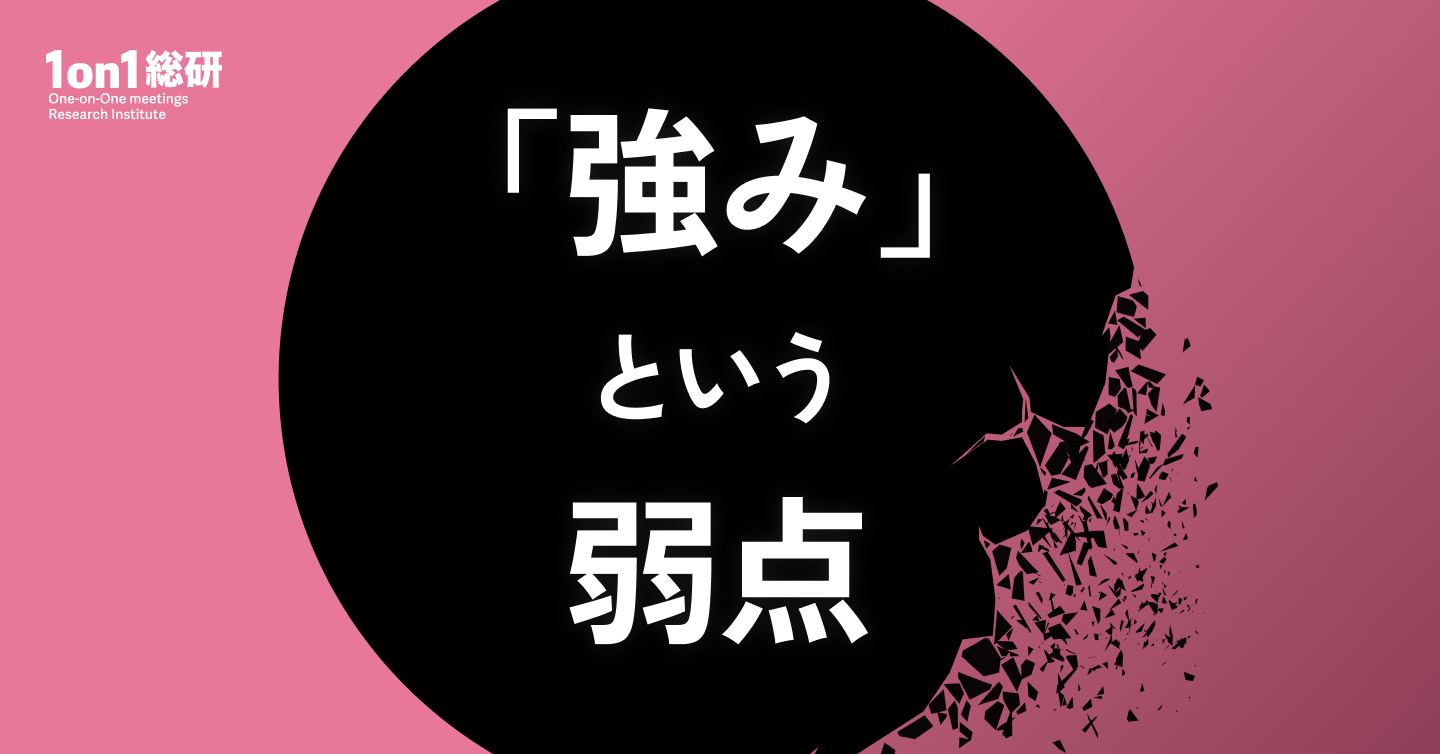
【失敗の本質】「勤勉な国」日本では世界に通用しない
2025年1月に永眠された野中郁次郎氏。共著「知識創造論」(東洋経済新報社)や知識マネジメントを扱った「SECIモデル」のみならず、「失敗の本質」(ダイヤモンド社)の共同著者としても有名です。ロングセラーとなった「失敗の本質」は、太平洋戦争での日本の敗戦について分析したものです。
野中郁次郎氏の功績を多角的に深掘りする本特集の前編と中編では、高度経済成長期の日本の製造業の強みが、野中氏が確立した知識創造モデルを通じて、アメリカのソフトウエア開発やスタートアップビジネスにも応用されてきたことを紹介しました。
ということは、日本のものづくり企業の強みが、時代を超えて海を越えて業種を超えても通用する。つまり、本質的な強みには業種などを問わずに「普遍性」があるということです。
逆に、日本が抱える普遍的な弱みや課題とは何でしょうか。そのヒントが書籍「失敗の本質」に眠っているのです。
先にその一端を紹介すると、日本の課題とは、人材の「質の高さ」や「勤勉性」への過剰な依存です。本来は「強み」であるはずが、場合によっては「弱み」に転じるのです。
今でいうと、「人が中心」を標語とする人的資本経営に対する一つの警鐘ともいえるこのテーマを深掘りします。
スターリンが聞いた日本の弱点
「失敗の本質」は、戸部良一、寺本義也 、鎌田伸一 、杉之尾孝生、村井友秀 、野中郁次郎の6氏による共著の書籍です。2005年にはこの6人による姉妹本「戦略の本質」(日本経済新聞出版)も上梓されました。いずれも過去の戦争を題材に、戦略のリーダーシップ、組織運営の巧拙を考察しています。
太平洋戦争における日本の敗因について洞察した「失敗の本質」では、ソ連軍が「日本軍の下士官兵や青年将校は優秀だが、高級将校は無能」だと、スターリンに報告したエピソードが印象的です。
戦いを個別にみるなら、日ごろの厳しい鍛錬によって磨き上げた力を発揮し、奇襲を受けたにもかかわらず、相手に大打撃を与えたといったような日本側の戦果もありました。その一方で、全体としては日本の「グランドデザインの欠如」を指摘しています。
ある戦いに臨む際、その目的は土地を確保するのか、相手の戦力を削ぐのか、相手の供給網を分断するのか、状況によって異なります。にもかかわらず、日本は目的を絞り込まず、複数の目的が混在した「玉虫色」の戦いがあったと指摘しています。
現代の企業経営でいうと、「現場レベルでは良い製品・サービスを提供しているのに、経営レベルの話となると、大局観がなく迷走している」といったところでしょうか。
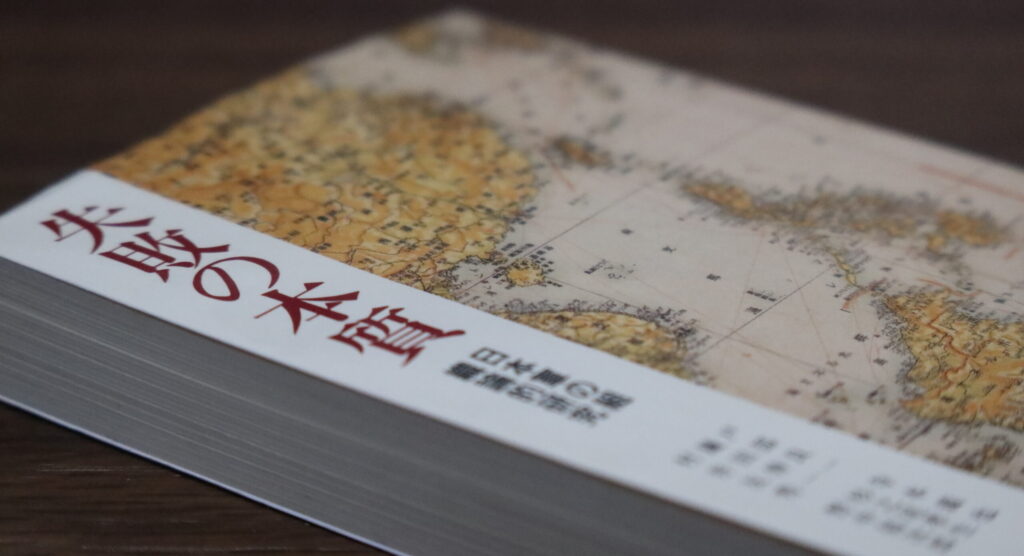
このほか、日露戦争での成功体験を捨てられずに大艦巨砲主義から脱却できず、また、諜報活動があまり重視されなかったとしています。明石元二郎らによる諜報活動が大いに機能した日露戦争とは対極的です。
こうした要因に加え、日本の「強み」や「美徳」に映ることが、逆に日本の弱みとあった点を失敗の本質ではいみじくも指摘しています。
それは「個人能力が高い」がゆえに属人化や部分最適に陥ってしまったこと、また献身性が勢い余って「月月火水木金金」に代表される自己犠牲を厭(いと)わぬ精神論がまかり通ってしまったこと。
その一方で、標準化や規格化による「全体最適」という概念が希薄であったことです。
持続可能性に欠く「玄人志向」
日本の主力戦闘機といえば零式艦上戦闘機、通称「零戦(ゼロ戦)」。日本の匠の技でしか実現しえなかった名機と言えば聞こえがいいものの、それが仇(あだ)にもなりました。
長い航続距離や俊敏性に優れている零戦には、軽量性に優れる合金「超々ジュラルミン」が採用されました。加工が難しいことで知られるこの材料は、高度な技能を持つ職人がいたからこそ扱えました。
しかし、高い技能が要求されるがゆえに「量産性」、つまり生産スピードの面では劣りました。製造が難しいだけでなく、「失敗の本質」によれば、飛行士に対してもその操作に「名人芸」を要求したとあります。
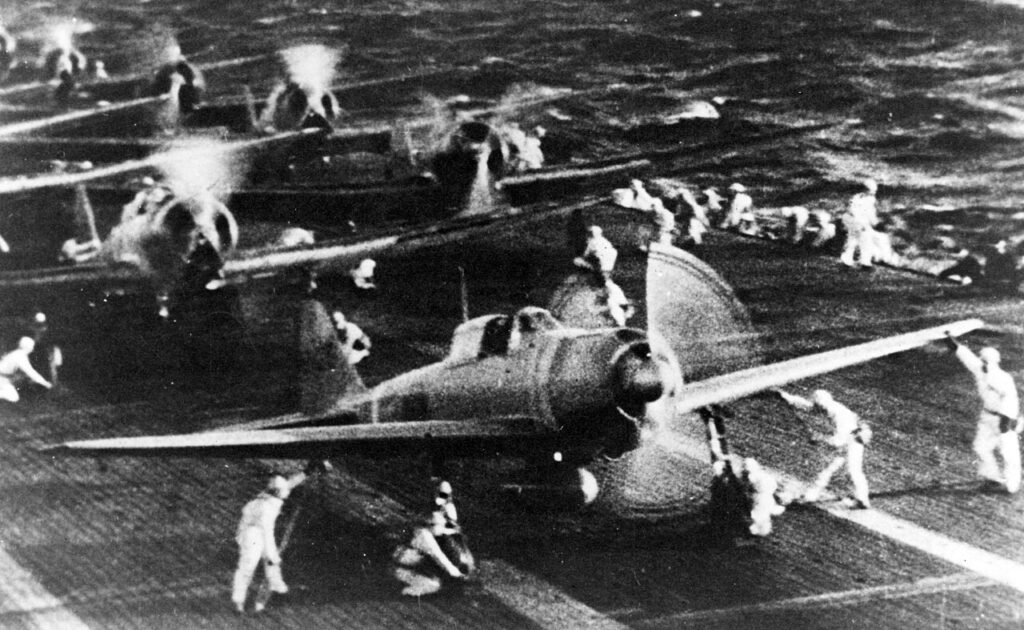
かたや米国の戦闘機「グラマンF6Fヘルキャット」では、製造手法が標準化されており量産しやすいというメリットがありました。しかも、米国では高度な技術を開発するにしても、平均的な能力を持つ人が問題なく操作できることを何より重視しました。
大戦では物量がモノを言います。損害が広がっていけば、兵器の大量生産による補充が必要となり、熟練したベテランではなく未熟な新人を投入する必要が生じます。
緒戦では問題にならなくとも、消耗戦に移行すると、零戦は作るにも使うにも「玄人」向けである点が大きなハンディキャップとなりました。
「失敗の本質」では、組織化された現代戦の成功に必要不可欠な「High Level of Mediocrity(高度の平凡性)」が欠けていた点に触れています。これは、平均的な能力を持つ人がやれることの水準を高めるという凡人を前提としたマネジメントです。
工業品ではなく、もはや工芸品
また、太平洋戦争で日本は実に多種多様な兵器を作りました。「失敗の本質」によれば、潜水艦「伊号」では27もの艦型が開発され、1艦型当たりの平均建造量はわずか4.2隻にとどまりました。今でいうところの「多品種少量生産」です。
この点については、東京大学および大阪大学の名誉教授である木村英紀氏が2009年に世に出した書籍「ものつくり敗戦」(日経BP)に詳しく描かれています。
この本によれば、戦前から日本は大量生産の前提である「規格化」が大きく遅れました。結果、やすりなどの手作業工具を使って器用に部品を手直しをし、部品同士の「すり合わせ(微調整)」をするなどの個人の「熟練」にゆだねられました。
陸軍が使っていた「三八式歩兵銃」でも、製造に工作機械を用いていたとはいえ、職人が一丁ずつ部品を調整する必要があり、なんと部品の「互換性」は同じ工場で作る製品間でしかなかったそうです。
そして潜水艦と同様に、海軍だけでも約30種類の機関銃と約120種類もの弾薬という、驚くほど多くの種類が作られました。
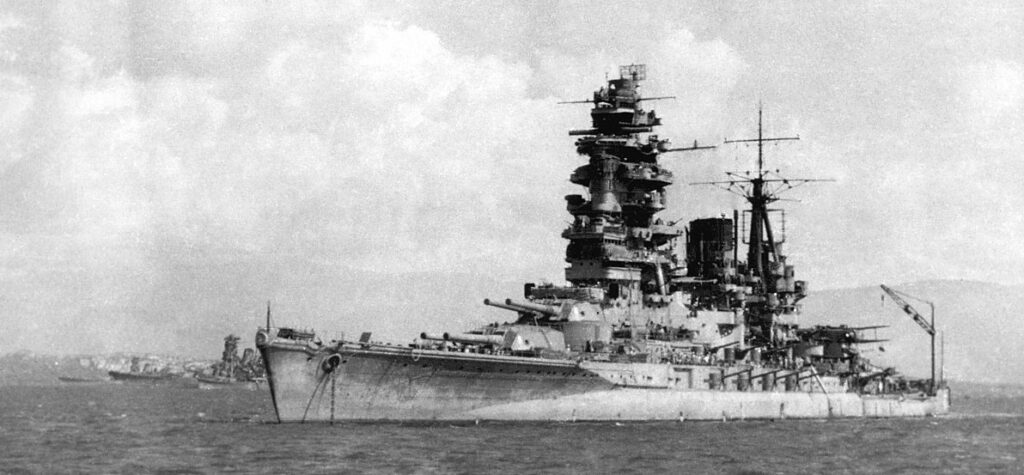
かたや英米では、高い精度で物を作れる熟練工が不足していました。そこで進めたのが規格化。ネジなどを共通化していけば、機械でも加工や組付けがしやすく、自動化も進めやすくなります。
日本が作っている飛行機や戦艦、銃は「工業品」よりも「工芸品」に近いものがあります。絵画や骨董品ならまだしも、戦時中のように人手が足りなくなり、非熟練者でも一定の品質にまとめることが求められる状況では不利に働きました。
半導体敗戦の本質
以上のことは、現代の私たちビジネスパーソンと仕事でも心当たりがあるのではないでしょうか。
日本の課題がビジネスに顕著に現れた例が、半導体に詳しい湯之上隆氏による著書「日本型モノづくりの敗北」(文藝春秋)に載っています。
同書によると、NECや日立製作所などの半導体事業が合弁して誕生したエルピーダ(後に米マイクロンが買収)では、NEC出身の技術者は全ての条件をしらみつぶしに調べるので早朝から深夜まで、それも土日を含めて働いていたそうです。
また同じ業界なのに、NECと日立製作所との間で「翻訳語集」が作成されるほど同じ言葉に対する解釈が違ったとか。
まさに「月月火水木金金」の精神や、工場が違うと互換性を保てなかった三八式歩兵銃の例を彷彿させます。
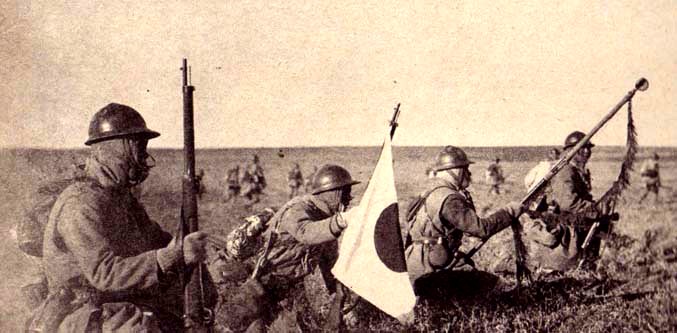
半導体製造装置においても興味深い考察があります。かつて、「露光機」と呼ばれる装置では1990年代まで、日本のニコンとキヤノンがほぼ市場を独占していました。
ただし、日本の露光機には「顔がある」と言われるほど、同じ品種でも1台ごとに「クセ」がありました。装置を別の工程に移すと品質に影響する可能性があるので、ある工程でしか使えない専用装置と化してしまいました。
そんな中、オランダの新興企業ASMLは、露光機のパーツ(モジュールと呼ばれる)の規格化を進めました。そして、アッセンブル(組み合わせる)する際、モジュール間の接続部を微調整をすることで装置ごとのクセを抑えました。
ASMLの機械を導入したのは、当時はまだ新興勢である台湾TSMCや韓国サムスン電子。両社の工場稼働率が95%と高かった理由は、製造装置が専用化せずに汎用的に使い回せたからです。
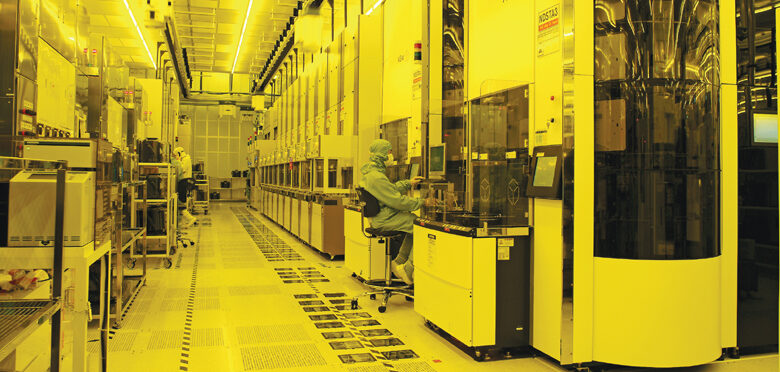
かたや専用機として使っている日本企業は、品質が高くても、時に稼働率50%に低迷することもあり、業績の足を引っ張りました。かくして、日本の半導体企業の地盤沈下は進み、併せてニコンとキヤノンも2000年代、ASMLにシェアの大逆転を許してしまいました。
「死の行進」の日の丸IT
ものづくりだけではありません。国際的な存在感が特に低い日本のソフトウェア産業もまた、標準化の概念が希薄なことで有名です。
最近の例では、2025年2月にNHKが日本IBMに対し、委託していたシステム開発の大幅遅延などを巡り東京地方裁判所に損害賠償を提訴した件が挙げられます。
提訴を受けた日本IBMは声明文を公表し、「提案時に取得した要求仕様書では把握できない、長年の利用の中で複雑に作り込まれた構造となっていることが判明した」と記載しました。NHKならではの「複雑に作りこまれた構造」によって、開発遅延を余儀なくされたという主張です。
それに先立つ2025年1月、ITシステム開発の頓挫を巡って日本IBMが文化シヤッターに損害賠償金約20億円の支払うように命じる判決が確定。ここでも標準的なITシステムを文化シヤッターの固有事情に合わせてカスタマイズを過度に進めた結果、実運用が困難な状況に陥ってしまいました。
このように、日本企業は自社独自のITシステムを要求し、その受託先のシステムインテグレーターと呼ばれるIT企業は、その要求を丸呑みしてしまう......その結果、システム開発と運用が行き詰まる事例が枚挙にいとまがありません。
それでも、労働供給力に余裕があった過去の時代には、開発現場の泊まり込みを含めて月火水木金金の精神で「デスマーチ(無理難題のプロジェクト)」を乗り切ってきました。
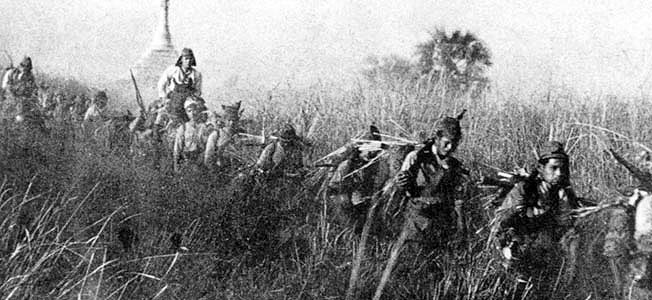
ソフトウェアでは優れた標準品を確立すれば、それを複製(コピー)するコストはほとんどかからない「限界費用ゼロ」の世界。ゆえにハードウェアにもまして標準化が重要であるにもかかわらず、日本はカスタム地獄に陥り、ソフトならではの拡張性というメリットを引き出せませんでした。
その弊害はITシステムのユーザー企業のみならず、提供(ベンダー)側にも及びます。顧客ごとにいちいちカスタム対応する手間がかかるので、標準ソフトをほぼそのままの仕様で幅広く企業に提供する欧米企業よりも、圧倒的に生産性が低くなります。
かくして日本からグローバルプレイヤーはほとんど生まれず、「ウィンドウズ」や「iOS」などの基本ソフト(OS)、検索エンジンをアメリカに抑えられているほか、ERP(統合基幹業務システム)やCAD(工業用設計ソフト)においてもアメリカおよび欧州の企業に圧倒されています。
今やデジタル・ソフト領域で5兆円を超える国際収支の赤字を出して「DX赤字」や「デジタル小作人」などと呼ばれるありさまです。
もっとも、日本企業も過去の反省を踏まえて標準化の取り組みは意識しており、遅まきながらも挽回なるか、今後に期待したい状況です。
人的資本時代への教訓
日本企業の全てが属人化やカスタム化による個別最適化に陥ってきたのではありません。
前回記事で取り上げたトヨタ生産方式は「平準化」の考えをベースにしています。作業が速い人ではなく、作業が遅い、もしくはミスが多い人に焦点を当て、作業が遅い・ミスする人でも問題なく作業ができるように仕組みを改善していきます。
その基本思想は「仕事を楽にする」こと。きつい作業や難しい作業は楽にすれば、疲れにくくミスも減るので、生産性は上がります。気合と根性で乗り越えようとするのとは対極的な発想で、先述の「高度の平凡性」と相通じるものがあります。
トヨタ生産方式だけではありません。例えば、無印良品も業務マニュアル「MUJIGRAM(ムジグラム)」を作り、店舗が違っても運営の標準化を徹底していることで知られています。
マニュアルとはいえ、「絶対」的な存在ではありません。無印良品では現場現場から上がった改善提案は全体最適の観点で検討され、提案が採用されればマニュアルに反映されていきます。
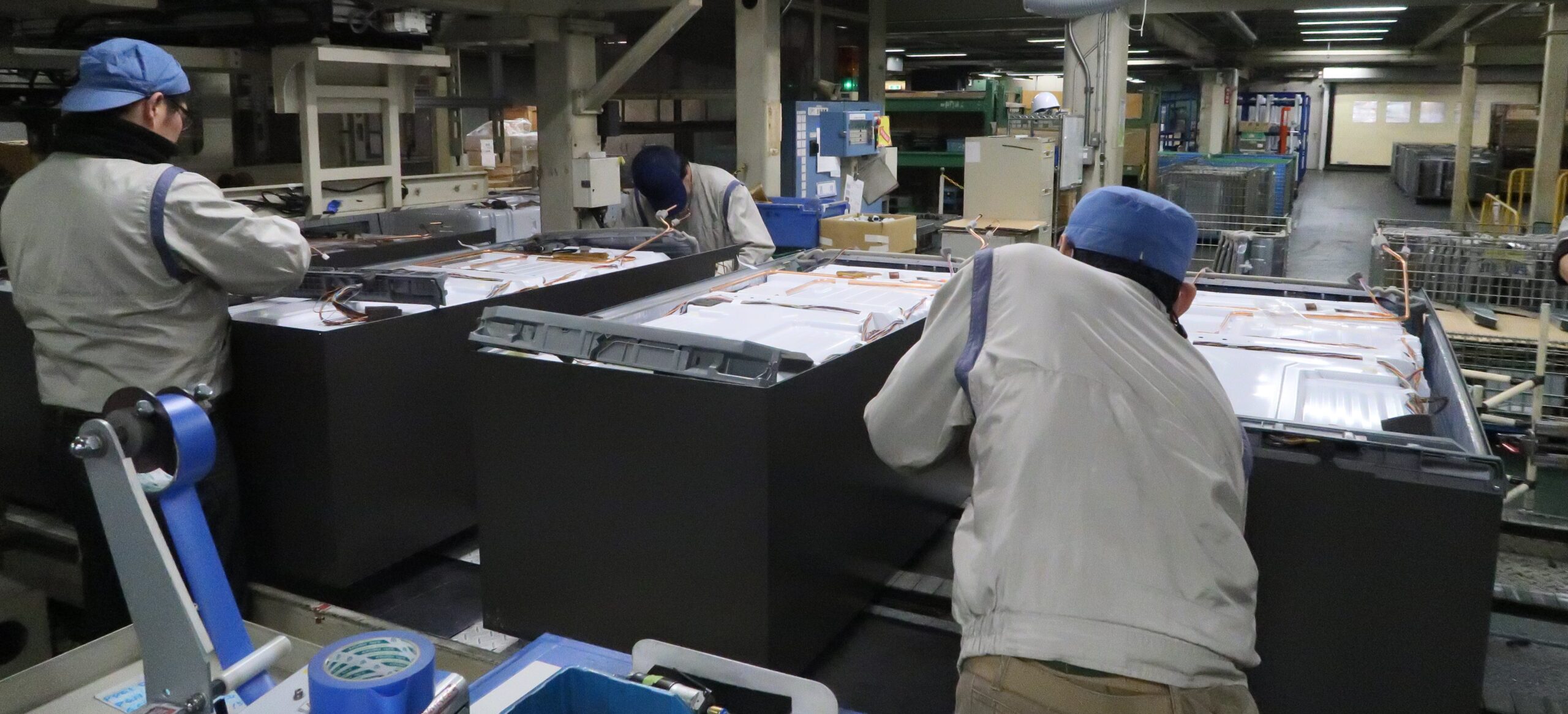
「無印良品は、仕組みが9割」(角川書店)の著者で、良品計画の松井忠三元社長・会長は、「全店規模でPDCAサイクルを回している状態です。かつ、全従業員に業務基準が100%浸透することが重要」だと、過去のインタビュー(*)で話しています。
今後は人手不足が深刻化し、「匠」のような個人技に依存した組織運営は持続不可能。「月月火水木金金」の精神で乗り越える発想はもってのほかです。
こうした議論は、今広がっている「人的資本経営」のあり方にも一石投じます。よく使われる「人が中心」、「人財」といったフレーズも解釈を誤ると、かつてのような属人性や個人の頑張りに依存した組織運営を再評価することになります。それでは、これまで説明したような部分最適に陥ってしまいます。
組織である以上は、トヨタ生産方式のように何らかの標準化や規格化、ルール化が必要になるでしょう。そのうえで、そのルールを柔軟に更新(アップデート)していければ変化に強い組織になります。このルールのアップデートを担う人材を育てていく。これこそが人的資本経営です。
*参考記事
サービス産業の「業務仕組み化」:「MUJIGRAM」を開発した無印良品・松井元会長インタビュー(サービス産業生産性協議会)
スターリンが聞いた日本の弱点
「失敗の本質」は、戸部良一、寺本義也 、鎌田伸一 、杉之尾孝生、村井友秀 、野中郁次郎の6氏による共著の書籍です。2005年にはこの6人による姉妹本「戦略の本質」(日本経済新聞出版)も上梓されました。いずれも過去の戦争を題材に、戦略のリーダーシップ、組織運営の巧拙を考察しています。
太平洋戦争における日本の敗因について洞察した「失敗の本質」では、ソ連軍が「日本軍の下士官兵や青年将校は優秀だが、高級将校は無能」だと、スターリンに報告したエピソードが印象的です。
戦いを個別にみるなら、日ごろの厳しい鍛錬によって磨き上げた力を発揮し、奇襲を受けたにもかかわらず、相手に大打撃を与えたといったような日本側の戦果もありました。その一方で、全体としては日本の「グランドデザインの欠如」を指摘しています。
ある戦いに臨む際、その目的は土地を確保するのか、相手の戦力を削ぐのか、相手の供給網を分断するのか、状況によって異なります。にもかかわらず、日本は目的を絞り込まず、複数の目的が混在した「玉虫色」の戦いがあったと指摘しています。
現代の企業経営でいうと、「現場レベルでは良い製品・サービスを提供しているのに、経営レベルの話となると、大局観がなく迷走している」といったところでしょうか。
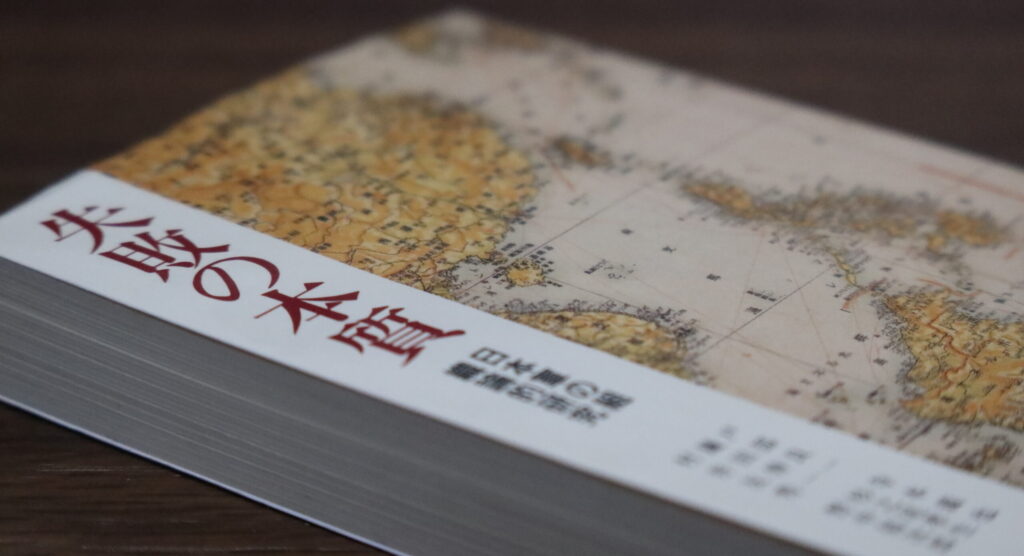
このほか、日露戦争での成功体験を捨てられずに大艦巨砲主義から脱却できず、また、諜報活動があまり重視されなかったとしています。明石元二郎らによる諜報活動が大いに機能した日露戦争とは対極的です。
こうした要因に加え、日本の「強み」や「美徳」に映ることが、逆に日本の弱みとあった点を失敗の本質ではいみじくも指摘しています。
それは「個人能力が高い」がゆえに属人化や部分最適に陥ってしまったこと、また献身性が勢い余って「月月火水木金金」に代表される自己犠牲を厭(いと)わぬ精神論がまかり通ってしまったこと。
その一方で、標準化や規格化による「全体最適」という概念が希薄であったことです。
持続可能性に欠く「玄人志向」
日本の主力戦闘機といえば零式艦上戦闘機、通称「零戦(ゼロ戦)」。日本の匠の技でしか実現しえなかった名機と言えば聞こえがいいものの、それが仇(あだ)にもなりました。
長い航続距離や俊敏性に優れている零戦には、軽量性に優れる合金「超々ジュラルミン」が採用されました。加工が難しいことで知られるこの材料は、高度な技能を持つ職人がいたからこそ扱えました。
しかし、高い技能が要求されるがゆえに「量産性」、つまり生産スピードの面では劣りました。製造が難しいだけでなく、「失敗の本質」によれば、飛行士に対してもその操作に「名人芸」を要求したとあります。
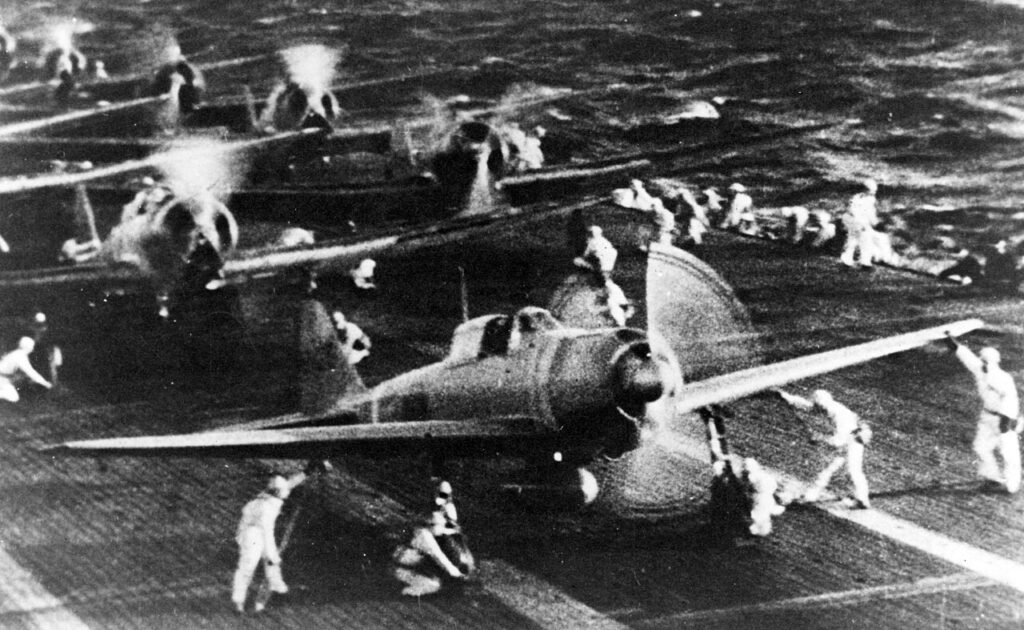
かたや米国の戦闘機「グラマンF6Fヘルキャット」では、製造手法が標準化されており量産しやすいというメリットがありました。しかも、米国では高度な技術を開発するにしても、平均的な能力を持つ人が問題なく操作できることを何より重視しました。
大戦では物量がモノを言います。損害が広がっていけば、兵器の大量生産による補充が必要となり、熟練したベテランではなく未熟な新人を投入する必要が生じます。
緒戦では問題にならなくとも、消耗戦に移行すると、零戦は作るにも使うにも「玄人」向けである点が大きなハンディキャップとなりました。
「失敗の本質」では、組織化された現代戦の成功に必要不可欠な「High Level of Mediocrity(高度の平凡性)」が欠けていた点に触れています。これは、平均的な能力を持つ人がやれることの水準を高めるという凡人を前提としたマネジメントです。
工業品ではなく、もはや工芸品
また、太平洋戦争で日本は実に多種多様な兵器を作りました。「失敗の本質」によれば、潜水艦「伊号」では27もの艦型が開発され、1艦型当たりの平均建造量はわずか4.2隻にとどまりました。今でいうところの「多品種少量生産」です。
この点については、東京大学および大阪大学の名誉教授である木村英紀氏が2009年に世に出した書籍「ものつくり敗戦」(日経BP)に詳しく描かれています。
この本によれば、戦前から日本は大量生産の前提である「規格化」が大きく遅れました。結果、やすりなどの手作業工具を使って器用に部品を手直しをし、部品同士の「すり合わせ(微調整)」をするなどの個人の「熟練」にゆだねられました。
陸軍が使っていた「三八式歩兵銃」でも、製造に工作機械を用いていたとはいえ、職人が一丁ずつ部品を調整する必要があり、なんと部品の「互換性」は同じ工場で作る製品間でしかなかったそうです。
そして潜水艦と同様に、海軍だけでも約30種類の機関銃と約120種類もの弾薬という、驚くほど多くの種類が作られました。
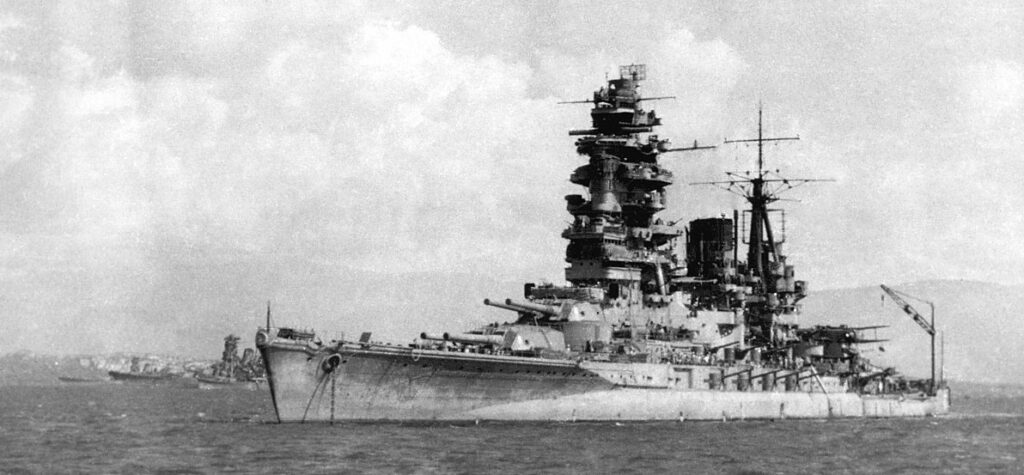
かたや英米では、高い精度で物を作れる熟練工が不足していました。そこで進めたのが規格化。ネジなどを共通化していけば、機械でも加工や組付けがしやすく、自動化も進めやすくなります。
日本が作っている飛行機や戦艦、銃は「工業品」よりも「工芸品」に近いものがあります。絵画や骨董品ならまだしも、戦時中のように人手が足りなくなり、非熟練者でも一定の品質にまとめることが求められる状況では不利に働きました。
半導体敗戦の本質
以上のことは、現代の私たちビジネスパーソンと仕事でも心当たりがあるのではないでしょうか。
日本の課題がビジネスに顕著に現れた例が、半導体に詳しい湯之上隆氏による著書「日本型モノづくりの敗北」(文藝春秋)に載っています。
同書によると、NECや日立製作所などの半導体事業が合弁して誕生したエルピーダ(後に米マイクロンが買収)では、NEC出身の技術者は全ての条件をしらみつぶしに調べるので早朝から深夜まで、それも土日を含めて働いていたそうです。
また同じ業界なのに、NECと日立製作所との間で「翻訳語集」が作成されるほど同じ言葉に対する解釈が違ったとか。
まさに「月月火水木金金」の精神や、工場が違うと互換性を保てなかった三八式歩兵銃の例を彷彿させます。
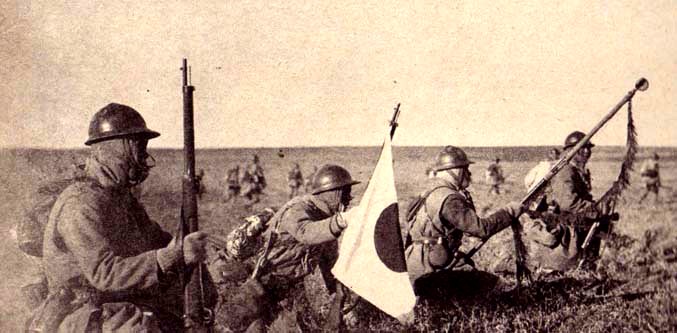
半導体製造装置においても興味深い考察があります。かつて、「露光機」と呼ばれる装置では1990年代まで、日本のニコンとキヤノンがほぼ市場を独占していました。
ただし、日本の露光機には「顔がある」と言われるほど、同じ品種でも1台ごとに「クセ」がありました。装置を別の工程に移すと品質に影響する可能性があるので、ある工程でしか使えない専用装置と化してしまいました。
そんな中、オランダの新興企業ASMLは、露光機のパーツ(モジュールと呼ばれる)の規格化を進めました。そして、アッセンブル(組み合わせる)する際、モジュール間の接続部を微調整をすることで装置ごとのクセを抑えました。
ASMLの機械を導入したのは、当時はまだ新興勢である台湾TSMCや韓国サムスン電子。両社の工場稼働率が95%と高かった理由は、製造装置が専用化せずに汎用的に使い回せたからです。
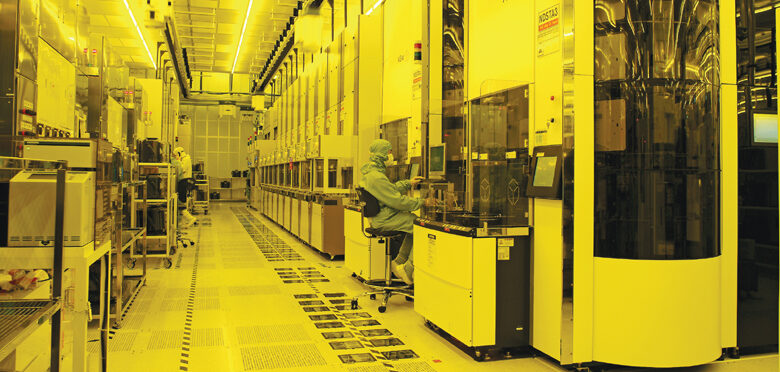
かたや専用機として使っている日本企業は、品質が高くても、時に稼働率50%に低迷することもあり、業績の足を引っ張りました。かくして、日本の半導体企業の地盤沈下は進み、併せてニコンとキヤノンも2000年代、ASMLにシェアの大逆転を許してしまいました。
「死の行進」の日の丸IT
ものづくりだけではありません。国際的な存在感が特に低い日本のソフトウェア産業もまた、標準化の概念が希薄なことで有名です。
最近の例では、2025年2月にNHKが日本IBMに対し、委託していたシステム開発の大幅遅延などを巡り東京地方裁判所に損害賠償を提訴した件が挙げられます。
提訴を受けた日本IBMは声明文を公表し、「提案時に取得した要求仕様書では把握できない、長年の利用の中で複雑に作り込まれた構造となっていることが判明した」と記載しました。NHKならではの「複雑に作りこまれた構造」によって、開発遅延を余儀なくされたという主張です。
それに先立つ2025年1月、ITシステム開発の頓挫を巡って日本IBMが文化シヤッターに損害賠償金約20億円の支払うように命じる判決が確定。ここでも標準的なITシステムを文化シヤッターの固有事情に合わせてカスタマイズを過度に進めた結果、実運用が困難な状況に陥ってしまいました。
このように、日本企業は自社独自のITシステムを要求し、その受託先のシステムインテグレーターと呼ばれるIT企業は、その要求を丸呑みしてしまう......その結果、システム開発と運用が行き詰まる事例が枚挙にいとまがありません。
それでも、労働供給力に余裕があった過去の時代には、開発現場の泊まり込みを含めて月火水木金金の精神で「デスマーチ(無理難題のプロジェクト)」を乗り切ってきました。
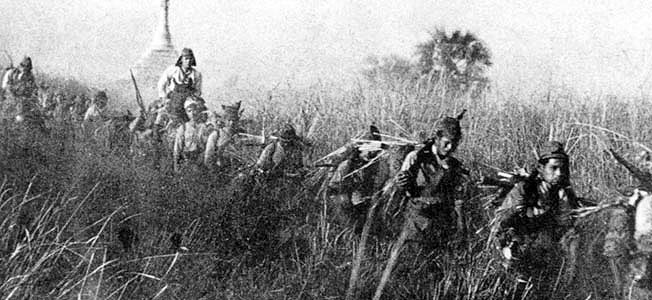
ソフトウェアでは優れた標準品を確立すれば、それを複製(コピー)するコストはほとんどかからない「限界費用ゼロ」の世界。ゆえにハードウェアにもまして標準化が重要であるにもかかわらず、日本はカスタム地獄に陥り、ソフトならではの拡張性というメリットを引き出せませんでした。
その弊害はITシステムのユーザー企業のみならず、提供(ベンダー)側にも及びます。顧客ごとにいちいちカスタム対応する手間がかかるので、標準ソフトをほぼそのままの仕様で幅広く企業に提供する欧米企業よりも、圧倒的に生産性が低くなります。
かくして日本からグローバルプレイヤーはほとんど生まれず、「ウィンドウズ」や「iOS」などの基本ソフト(OS)、検索エンジンをアメリカに抑えられているほか、ERP(統合基幹業務システム)やCAD(工業用設計ソフト)においてもアメリカおよび欧州の企業に圧倒されています。
今やデジタル・ソフト領域で5兆円を超える国際収支の赤字を出して「DX赤字」や「デジタル小作人」などと呼ばれるありさまです。
もっとも、日本企業も過去の反省を踏まえて標準化の取り組みは意識しており、遅まきながらも挽回なるか、今後に期待したい状況です。
人的資本時代への教訓
日本企業の全てが属人化やカスタム化による個別最適化に陥ってきたのではありません。
前回記事で取り上げたトヨタ生産方式は「平準化」の考えをベースにしています。作業が速い人ではなく、作業が遅い、もしくはミスが多い人に焦点を当て、作業が遅い・ミスする人でも問題なく作業ができるように仕組みを改善していきます。
その基本思想は「仕事を楽にする」こと。きつい作業や難しい作業は楽にすれば、疲れにくくミスも減るので、生産性は上がります。気合と根性で乗り越えようとするのとは対極的な発想で、先述の「高度の平凡性」と相通じるものがあります。
トヨタ生産方式だけではありません。例えば、無印良品も業務マニュアル「MUJIGRAM(ムジグラム)」を作り、店舗が違っても運営の標準化を徹底していることで知られています。
マニュアルとはいえ、「絶対」的な存在ではありません。無印良品では現場現場から上がった改善提案は全体最適の観点で検討され、提案が採用されればマニュアルに反映されていきます。
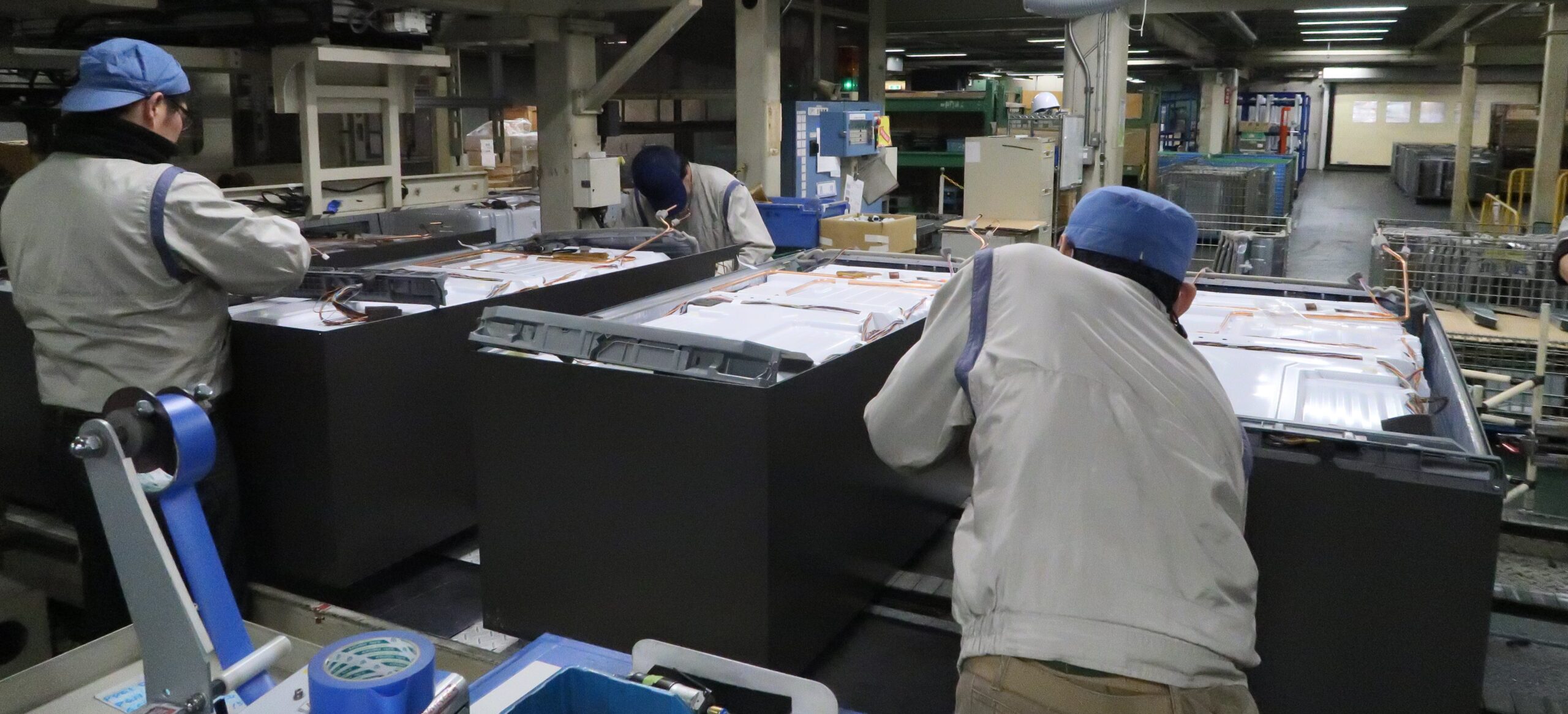
「無印良品は、仕組みが9割」(角川書店)の著者で、良品計画の松井忠三元社長・会長は、「全店規模でPDCAサイクルを回している状態です。かつ、全従業員に業務基準が100%浸透することが重要」だと、過去のインタビュー(*)で話しています。
今後は人手不足が深刻化し、「匠」のような個人技に依存した組織運営は持続不可能。「月月火水木金金」の精神で乗り越える発想はもってのほかです。
こうした議論は、今広がっている「人的資本経営」のあり方にも一石投じます。よく使われる「人が中心」、「人財」といったフレーズも解釈を誤ると、かつてのような属人性や個人の頑張りに依存した組織運営を再評価することになります。それでは、これまで説明したような部分最適に陥ってしまいます。
組織である以上は、トヨタ生産方式のように何らかの標準化や規格化、ルール化が必要になるでしょう。そのうえで、そのルールを柔軟に更新(アップデート)していければ変化に強い組織になります。このルールのアップデートを担う人材を育てていく。これこそが人的資本経営です。
*参考記事
サービス産業の「業務仕組み化」:「MUJIGRAM」を開発した無印良品・松井元会長インタビュー(サービス産業生産性協議会)
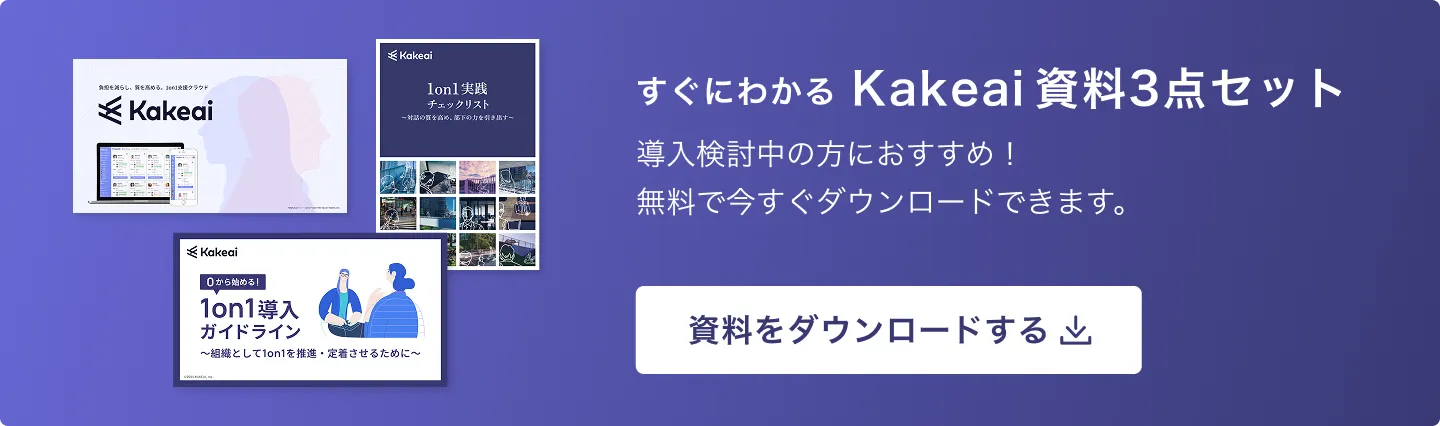
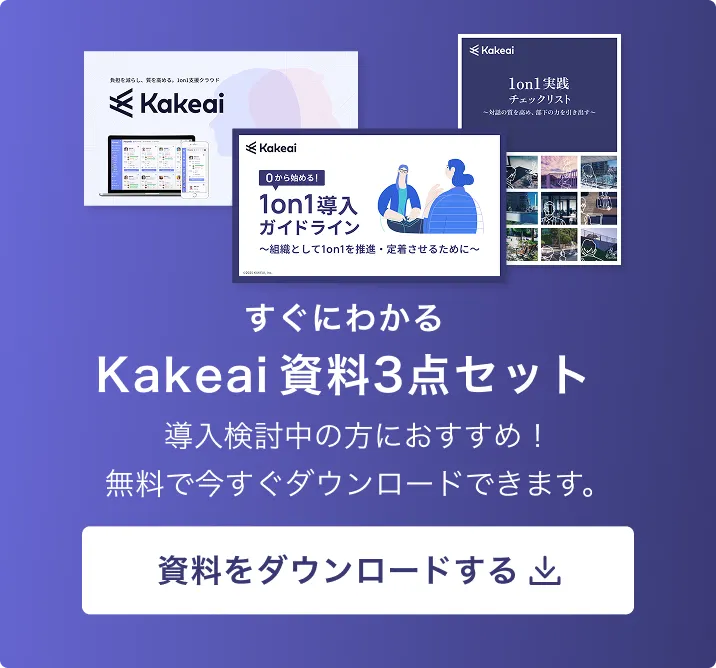
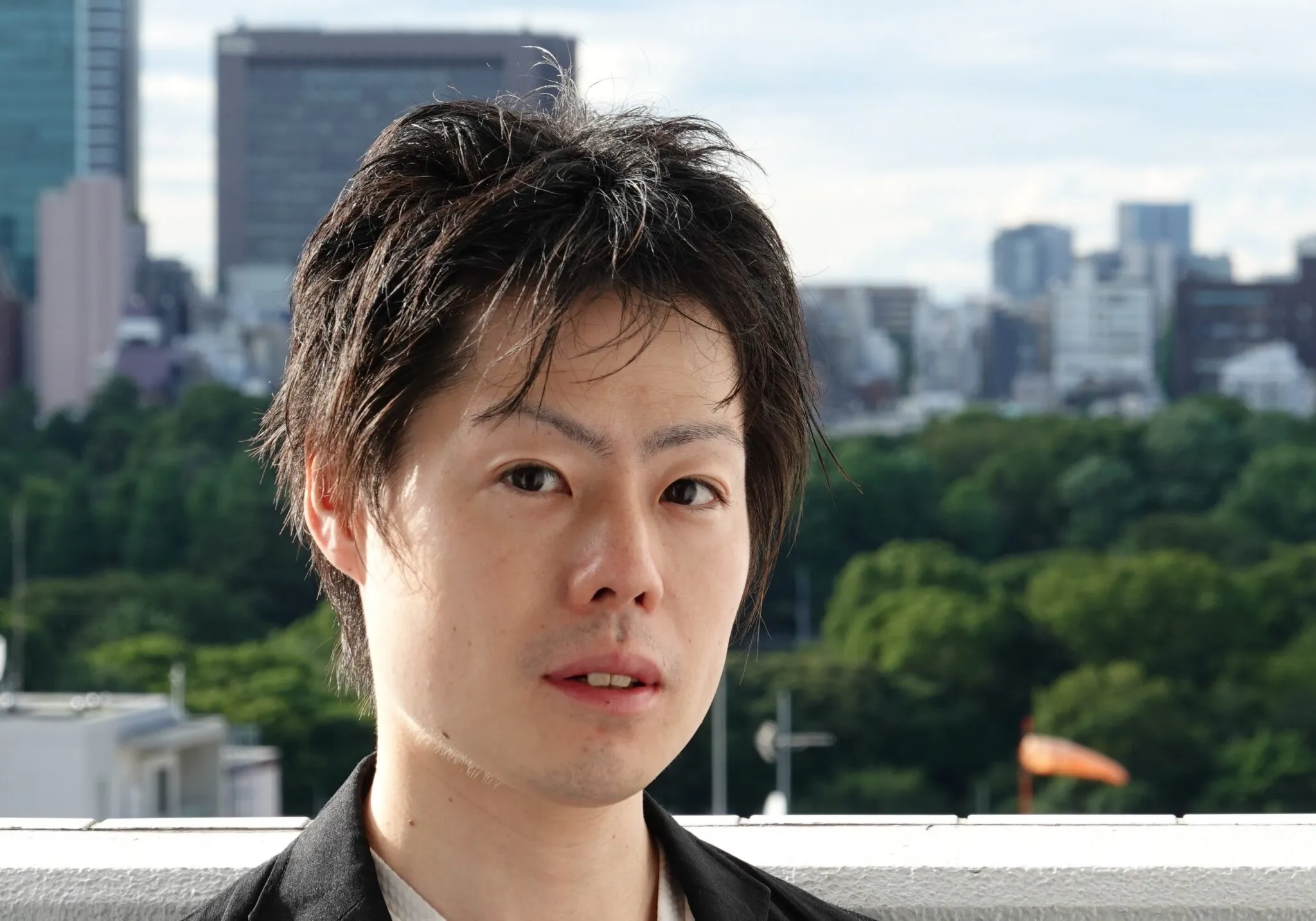